4 Easy Ways To Bring Lean To Your Work Floor
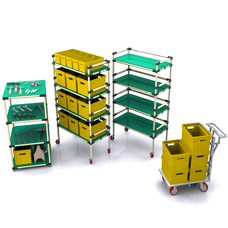
You may conceive of lean as a philosophy and methodology for large corporations, but it’s easier to implement and just as useful for small to mid-sized businesses. Regardless of your product, a philosophy of continuous improvement lets you streamline material handling, better organize production, and standardize procedures. Getting started with the philosophy that revved up Toyota’s production line can happen in stages. Here are a few simple ways to apply it to your manufacturing work floor.
Use Your Small Business Advantage
Leverage how easy it is to implement lean principles when it’s just you and your employees. Big businesses have to deal with multiple levels of management and staff, but you have direct communication in a small firm. You don’t need to hire an expert on the methodology, but you do need to make sure everyone receives a basic education in the Toyota way, especially the kaizen concept of small, incremental continuous improvements.
Set Improvement Goals
Set goals, but not a road map. You’ll discover problems as you go along. Creating a formal plan of problems to solve isn’t true lean application. Set goals and metrics up before beginning. Improvements that help you meet these goals, measured via your metrics are viable, valid improvements.
Organize and Standardize the Workspace
A clean, organized work place provides a better environment for efficiency. You should be able to, at a glance, reach any needed tool or material. You should also be able to tell what is missing. One tool set for implementing this visual standard, 5S tools, you probably already have on hand. 5S means sort, straighten, shine, standardize and sustain. You’ve probably seen or used a 5S cart before. Other tools to achieve organization include custom design carts or racks, connectors and pipes (or tubing) used to quickly construct modular units that enable continuous flow in the manufacturing environment. These same tools become a key of continuous improvements since they’re easily used to construct items like bump carts using simple pipe, connectors, and casters.
Create a Sustainable Company Philosophy.
You need more than momentary motivations like solving the first big problem. You need sustainable habits that make the Toyota way your company’s way permanently. Empower employees to suggest or implement fixes as long as they comply with safety requirements, such as those issued by the Occupational Safety and Health Administration (OSHA). Also, have company leaders implement and practice the philosophy.
Getting started with the Toyota way isn’t hard. Start small and encourage employees with visual success reminders. Post before and after photos of each work floor area. When everyone can see the results of the first area to undergo the 5S treatment, it becomes an achievement they can envision. Don’t try to 5S the whole plant at once. Tackle one area at a time. Provide the right tools for the job. Contact C Tek for help getting started with the right tools for continuously improving your plant floor. We can put customization in your hands.